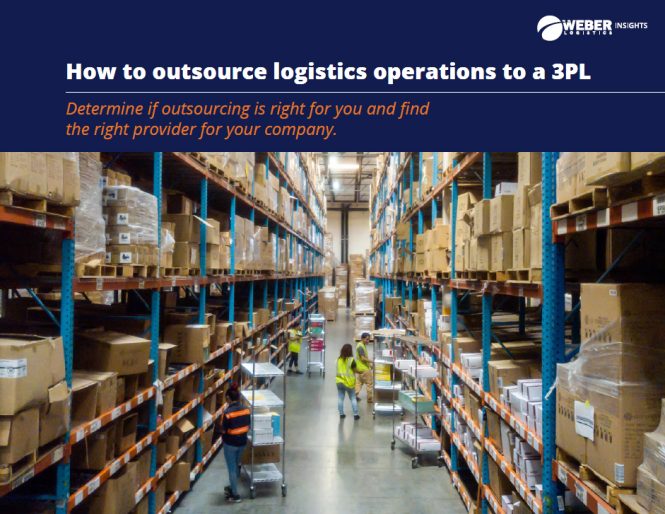
Outsourcing logistics and supply chain management is becoming increasingly crucial for businesses seeking to optimize operations and reduce costs. Global markets demand flexibility and responsiveness, making it challenging for companies to maintain in-house capabilities for every aspect of the supply chain. Outsourcing these tasks allows companies to focus on core competencies, leverage expert knowledge, and gain substantial cost savings while increasing efficiency. This article will explore the intricacies of outsourcing logistics and supply chain, identifying key benefits and highlighting best practices for optimizing operations and reducing costs in the supply chain. We’ll dive into strategies for selecting the right outsourcing partner, managing expectations, and continuously improving performance. We’ll also explore potential pitfalls to avoid, along with actionable steps to ensure a successful outsourcing initiative.
Understanding the Benefits of Outsourcing Logistics and Supply Chain
Optimizing Operations Through Expertise
Outsourcing logistics and supply chain functions to specialized third-party logistics (3PL) providers allows companies to tap into a wealth of experience and cutting-edge technology. These providers possess extensive knowledge of transportation networks, warehousing, inventory management, and global trade regulations. By leveraging their expertise, businesses can enhance operational efficiency, reduce costs, and free up internal resources for strategic initiatives. A well-structured outsourcing arrangement can substantially reduce operational overhead, allowing companies to dedicate their time and capital to innovation rather than complex logistical processes.
Reducing Costs and Improving Efficiency
Outsourcing often leads to significant cost reductions. By leveraging economies of scale and specialized resources, 3PL providers can negotiate favorable rates with carriers and streamline transportation processes. This can translate to substantial cost savings in areas such as transportation, warehousing, and inventory management. In addition to cost savings, companies can often achieve a greater level of efficiency, leading to faster order fulfillment times and increased customer satisfaction. A streamlined process can free up significant time and resources within a business, promoting a rapid and positive return on investment.
Enhanced Agility and Scalability
Outsourcing allows businesses to adapt quickly to market changes and fluctuations in demand. 3PL providers offer flexible solutions that can be scaled up or down as needed. This agility is especially crucial in a globalized economy where market demands can fluctuate frequently. By partnering with a flexible logistics provider, companies can ensure the ability to adjust to sudden shifts in demand. Outsourcing helps businesses to maintain an agile and responsive posture to the changing business needs.
Selecting the Right Outsourcing Partner
Establishing Clear Performance Metrics
Choosing the right outsourcing partner is critical for a successful outcome. Before entering into any agreement, establish clear performance metrics and service level agreements (SLAs). These SLAs will define specific expectations in areas such as on-time delivery, order fulfillment, and customer service. For instance, metrics like average transit time, order accuracy, and customer satisfaction scores should be clearly outlined. With clear expectations in place, both the company and the outsourcing provider can better measure success, fostering a positive working relationship.
Evaluating Provider Expertise and Reliability
Thoroughly evaluate potential outsourcing partners’ expertise and reliability. Investigate their experience in handling similar supply chains, their technology infrastructure, their financial stability, and their track record in customer satisfaction. Understanding their network of suppliers and carriers will also offer important insight into their proficiency. Conducting due diligence on potential partners is essential to ensure the success of an outsourcing arrangement.
Conducting a thorough due diligence and risk assessment process will provide necessary support for a smooth transition.
Managing Expectations and Maintaining Communication
Building Strong Communication Channels
Clear and consistent communication is paramount throughout the outsourcing relationship. Establish dedicated communication channels with the outsourcing provider to address any issues or concerns promptly. Regular meetings, progress reports, and feedback sessions are important for successful partnership. Maintaining effective communication fosters transparency and collaboration, contributing to a smooth and productive relationship.
Establishing Clear Roles and Responsibilities
Clearly define roles and responsibilities within the collaboration to avoid conflicts and ensure that everyone understands their individual contributions. A clearly defined structure enhances accountability and reduces ambiguity. This ensures that the outsourcing partner is working in alignment with the company’s goals and strategy.
Proactive Problem Solving
Establishing proactive problem-solving mechanisms is crucial to addressing challenges promptly and effectively. Designate personnel and create a formal procedure for identifying and resolving potential issues in a collaborative manner. Proactive problem solving will limit the impact of issues that arise, maintaining a healthy and productive partnership.
Continuous Improvement and Performance Evaluation
Implementing Continuous Improvement Strategies
Implementing continuous improvement strategies is vital for long-term success. Evaluate key performance indicators (KPIs) regularly to identify areas for enhancement in the logistics and supply chain processes. Regular reviews will allow for proactive management of potential issues and facilitate improvements in performance.
Tracking Key Performance Indicators (KPIs)
Track KPIs such as on-time delivery rates, inventory turnover, and transportation costs. These metrics will provide valuable insights into the efficiency and effectiveness of the outsourcing arrangement. Analyzing these metrics allows companies to understand the true cost and value derived from the outsourcing contract. This data-driven approach is vital to making informed decisions and continuously improving operational effectiveness.
Performance Review Meetings
Schedule regular performance review meetings to discuss progress, identify areas for improvement, and address any concerns. Use feedback to refine strategies and ensure that the outsourcing arrangement remains aligned with business objectives. Regularly revisiting KPIs with the outsourcing partner promotes continuous improvement and performance optimization.
Case Study: XYZ Corporation and ABC Logistics
Cost Reduction Through Outsourcing
XYZ Corporation, a multinational manufacturer, outsourced its logistics operations to ABC Logistics to reduce costs and improve efficiency. By leveraging ABC Logistics’ expertise in global supply chain management, XYZ Corporation achieved substantial cost savings on transportation and warehousing, while concurrently increasing the speed and accuracy of order fulfillment. These results led to a higher level of efficiency, saving the company significant time and resources.
Enhanced Agility in Response to Market Changes
XYZ Corporation now had increased responsiveness in responding to fluctuations in demand, resulting in a significant improvement in the speed and accuracy of order fulfillment. This flexibility allowed them to adapt to changing market conditions and capitalize on new opportunities.
Conclusion
XYZ Corporation’s decision to outsource its logistics functions was a strategic move that yielded substantial benefits in terms of cost reduction, increased efficiency, and enhanced responsiveness.
Frequently Asked Questions
What are the potential risks of outsourcing logistics and supply chain?
Outsourcing logistics and supply chain operations can carry some risks. A poorly chosen outsourcing partner can lead to service disruptions, loss of control over certain operations, and communication problems. Businesses must conduct thorough due diligence to select a reliable and capable partner to mitigate such risks. Transparency, clear communication, and well-defined contracts are critical to reducing potential risks.
How can I effectively manage the transition process when outsourcing logistics?
Managing the transition is a crucial step. A thorough transition plan should address all aspects of the handover, from data migration to training processes. Clearly defining roles and responsibilities, establishing communication channels, and setting up a reporting structure are important steps to a smooth transition to the outsourcing partner. Planning for potential disruptions and establishing contingency measures will help to ensure a seamless transfer of operations.
In conclusion, optimizing logistics and supply chain operations through outsourcing offers significant benefits for businesses. By strategically selecting a reliable outsourcing partner, companies can focus on their core competencies while achieving cost reductions, improved efficiency, and enhanced agility. This approach allows them to adapt to market fluctuations and maintain a competitive edge. For further improvements, ongoing monitoring and performance evaluation are crucial. We recommend companies to establish clear KPIs and regular communication with their outsourcing partners to ensure consistent alignment and optimal outcomes. Implementing these strategies leads to a streamlined and cost-effective supply chain, enhancing profitability and long-term success. Explore outsourcing logistics and supply chain solutions today for greater business efficiency!